Dental Crowns: What Do They Do and What Are They Made of?
Home » Traditional Lab Techniques » Dental Crowns: What Do They Do? What Are They Made Of?
Many of us have needed them. Whether it be from a chipped tooth, decay, a root canal or some other cosmetic measure, many of us have needed dental crowns or veneers.
Some offices offer same day crowns where the restoration is designed and milled in-house. Many others will send their cases out to a dental lab.
But what is a crown used for and how are they made?
What Is a Dental Crown?
A crown is an artificial tooth. Occasionally, a patient’s natural teeth are no longer able to handle the vigor and stresses of daily use. Reasons for needing a crown vary but in its simplest form, a dental crown is replacement tooth that can perform the function of a real tooth and appear natural.
What Are Crowns Made Of?
Currently there are three major restoration materials: porcelain ceramics, lithium disilicate, and zirconia.
PFM and PFZ
Porcelain crowns are the longest standing and most aesthetically pleasing of the three materials most used today. The process for creating a porcelain crown is a work intensive and detail-oriented endeavor.
The restoration begins with a model of the mouth and prepped tooth. Impressions of your mouth can be taken digitally with an intraoral scanner or traditionally with impression material and an impression tray. Once the lab tech has your impression, an exact model of your mouth is made.
After the model is made, the technician will create a coping to use as a base. Usually, the coping is made of a metal alloy (Porcelain Fused to Metal, PFM) but can also be milled from zirconia (Porcelain Fused to Zirconia, PFZ).
A material called opaque is used to build up the bulk of the crown on the coping. Opaque is similar to clay, think of a sculptor working with a sculpture. The tooth is shaped by the lab tech to the rough size the tooth needs to be before being fired in an oven to harden.
Once the opaque has been applied, liquid porcelain is applied layer by layer until the tooth is the appropriate size to correctly fit the model without interfering with the patient’s ability to chew or speak clearly.
Each layer of porcelain is applied and then hardened in an oven. Several layers are porcelain are typically needed before the final stain and glaze are applied.
The overall quality of the aesthetic is highly dependent on the skill of the technician. The overall strength of the crown is determined by the number of layers of porcelain and the quality of the firing process. Aesthetically speaking, an experienced lab tech can create truly stunning restorations that mimic natural teeth perfectly. Although they are structurally the weakest restorations, the beauty is unmatched.
Lithium Disilicate (Li-Di)
Li-Di crowns were created in the late 1980’s by Ivoclar-Vivident.1 Usually referred to as e.Max crowns, this revolutionary ceramic material offered many of the aesthetic qualities of porcelain, but improved the flexural strength.
Traditionally, Li-Di crowns were made by casting. After creating a model of the patient’s mouth, a lab technician would create a cast using wax investment.
The Li-Di material would be heated to a molten level in a sintering oven and pressed into the mold of the tooth.
The resulting crown would have the advantage of being a solid piece of material. This advancement removed the possibility of having layers of material cleave off the crown as was common with PFMs.
Although the aesthetics could not reach the height of a well-made porcelain crown, the superior strength made them the choice for anterior crowns for much of the next quarter century.
The process also removed the need to rely so heavily on the skill level of an individual technician.
Today, Li-Di crowns can be designed digitally and milled for improved accuracy.
Zirconia Restorations
Zirconium is a naturally occurring element, found in the Periodic Table of Elements with atomic number 40, and is classified as a transitional metal. When zirconium is combined with oxygen, it becomes zirconium oxide, also known as ZIRCONIA, a very biocompatible and strong ceramic.2
Zirconia was traditionally used for posterior restorations as early as the 1970’s because of its immense flexural strength. Unfortunately, the trade off for that much strength was poor light translucency, which resulted in poor aesthetics.
The general opinion for decades was zirconia was best used in the back of the mouth where it would not be visible and Li-Di crowns used for anterior teeth. Anterior teeth require less physical stress and aesthetics are much more important.
In the early 2000’s many companies revolutionized a new type of zirconia that dramatically increased translucency and allowed different degrees of shading to be used. Today, zirconia restorations are the most prescribed crowns and used regularly for anterior and posterior teeth.
Zirconia is designed with a CAD/CAM method (computer aided design/computer aided manufacturing). First a model of the patient’s mouth is scanned into a computer. Then, a lab technician designs the shape of the crown. That design is then sent to a mill where a crown is milled from a solid puck of zirconia.
The crowns are then sintered to ensure strength, and finally stained and glazed to achieve the aesthetics.
This streamlined process allows dentists the option to design and mill their crowns in-house using the CEREC chairside milling system. However, many dentists still prefer to leave the design to the professionals at a dental lab, such as Utica Dental Laboratory.
Gold Crowns
Some dentists still prefer to have crowns milled from gold or other precious metals. This technique was popular before the advent of different ceramic materials. The rising cost of metal has made this a bit cost prohibitive, but it is still an option.
Resources
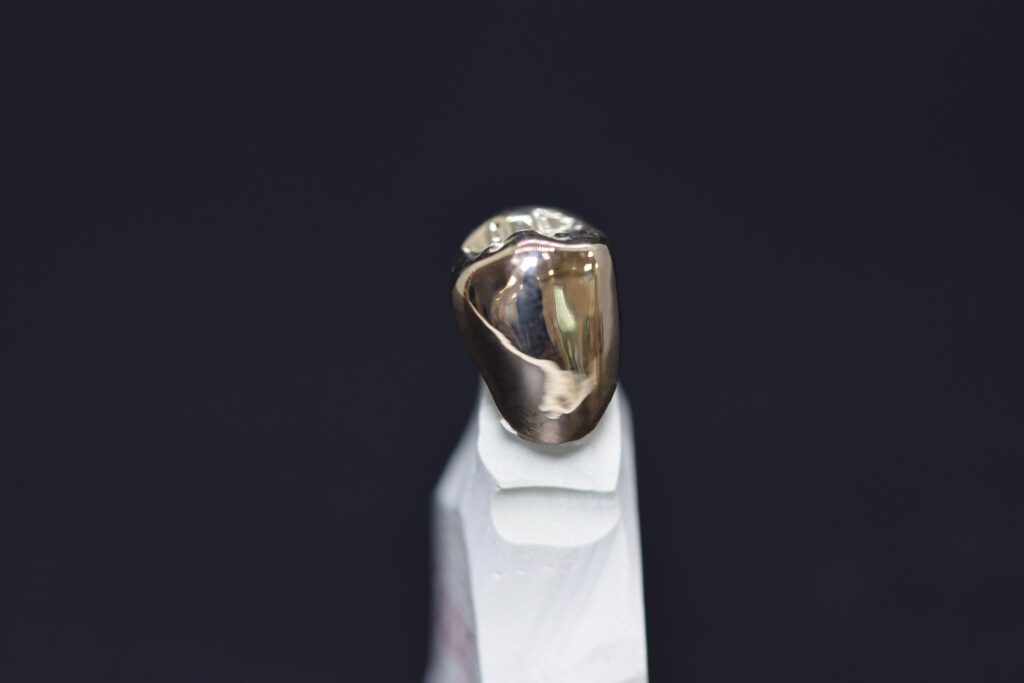
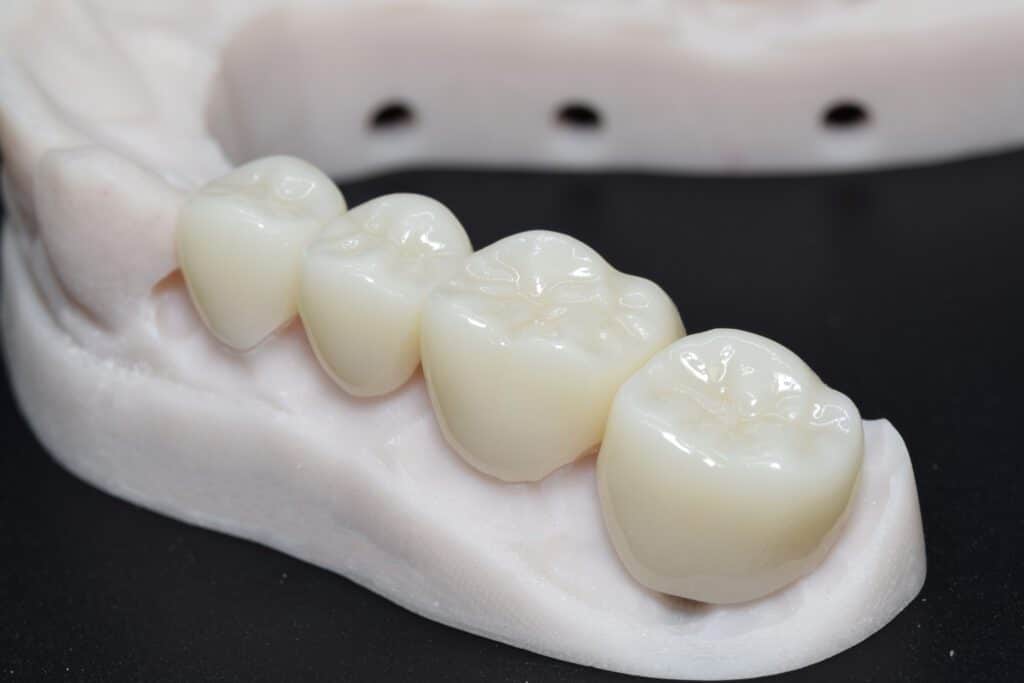