The past five years has seen a swathe of technological advancements in the dental laboratory. The long promised “digital revolution” appears to have finally taken hold. Just in time too.
The generation of craftsmen and women who so painstakingly perfected their craft in the dental lab are retiring and there aren’t many people in the next generation prepared to take their places.
Dental technology programs have all but disappeared and few dental labs are big enough or stable enough to implement the resources required to train and hone the skill required in-house.
Many dental laboratories have been forced to look elsewhere for ways to apply variations of restoration techniques that were once a mainstay for any dental lab. Many more have closed their doors or sold their businesses as retirement neared.
It is increasingly difficult to find a lab capable of producing a high-quality porcelain restoration. Likewise with removable, traditional dentures. Porcelain restorations may be completely phased out within the next decade.
So, what now and what’s next? The market for dental lab services is expected to grow 5.5% over the next 6 years. How will the industry cope with an ongoing employment crisis?
3D Printing, Scanning and Design in the Dental Laboratory
A true digital workflow involves intra oral scans, CAD/CAM design, and 3D printing or some other automated manufacturing technique (milling). Intra-oral scanner quality has increased considerably since its creation in the late 1980’s. Accessibility for scanners as also increased dramatically. While still costing a pretty penny, an increase in competition has seen the overall affordability come in line with the typical dental professional.
Scan quality has also dramatically improved over the past decade. While operator error will always remain an issue, the device itself is capable of taking an accurate scan at near a 100% success rate for teeth prepped for crowns and bridges, as well as full arch scans for night guards and retainers.
While soft tissue scans of edentulous patients are possible, more care must be taken. Most scanners possess the ability to capture an accurate scan, but errors are common. Careful reviews of each intraoral scan is required before sending to the dental lab.
The design process is where the next generation of dental technology really shines. It man have taken years or even decades for a dental lab technician to master the intricacies of tooth anatomy, stain and glaze shading, and the process of controlling material shrinkage when building a porcelain crown. Likewise with understating the nuanced details when building a wax model for dentures.
CAD/CAM design software takes a lot of the guess work out of design. What was once left up to the careful eye and craftsmanship of the lab tech is now digitally rendered in minutes. So long as accurate models are scanned and the proper articulation is achieved, 80% of the design process is completed immediately.
There is still some nuanced detailed that needs to be applied, especially in crown design. But the stage where most mistakes are made regarding fit is largely automated.
The same is true when digitally designing a denture. Lab techs no longer need to estimate denture thickness and manually apply wax to create a cast for dentures. Once an edentulous model is scanned, the design software will determine the proper thickness. And, if adjustments need to be made, it’s as easy as manually entering how thick you’d like the denture on a computer screen.
3D Printing Increases Efficiency and Decreases Dental Lab Waste
3D printing is an additive process. While metal 3D printers do exist and are used in the dental industry, most applications apply to removable prosthodontics. It has only been over the past two years that resin has been developed to adequately replace Lucitone acrylic.
Indeed, the last hurdle for 3D printed dentures was a development of a resin that was as strong as acrylic and at least as aesthetically appealing as it.
Now, pink denture bases can be printed and combined with tooth colored 3D printed denture teeth.
3D resin is a liquid when stored. The genius is involved with the manufacturing. With each passing layer, a UV light is used to trace the design of the denture, teeth, or other apparatus.
The resin is photosensitive, the UV light soft cures the resin enough for a form to take shape. After each pass with the UV light, the printer base is raised, and a new layer is formed on top of the previous layer.
Once the denture base and teeth have been printed, they are combined and tacked in place using additional resin, then hard cured in a UV oven. The heat and light of the oven causes the denture base to shrink around the denture teeth, thus binding them in place.
3D Printed Dental Crowns and Ceramics Still Far Off
Long lasting, permanent dental crown resin is currently being marketed by a number of 3D printing companies. However, the material used to create the resin is still large chain polymers, cured with UV light.
While I don’t don’t doubt the material is safe to use and long lasting, the aesthetics of a 3D printed polymer crown can not compare to ceramics.
There are currently several manufacturers working to develop a 3D printer capable of printing a material similar to Lithium-Disilicate or Zirconia. However, word on that progress is scarce. It is generally unwise to doubt the advancements that can be made in dental and medical technology. But the hurdles of creating a material hard enough and translucent enough to pass as a natural tooth are significant.
Zirconia is Increasing in Popularity, As Well As in Aesthetics
While additive manufacturing processes for crown and bridge may still be far off, the zirconia that is milled is becoming more and more lifelike. The removable side of the dental lab has lagged a bit behind in terms of its digital capability. Utica Dental Lab has been designing and milling zirconia restorations for well over a decade.
Once thought to be structurally sound but aesthetically unacceptable, new multilayered zirconia from e.Max and Bruxzir will be the most likely candidates for replacing porcelain crowns and veneers.
Check out our Advancements in Digital Dentistry YouTube Series for more information!
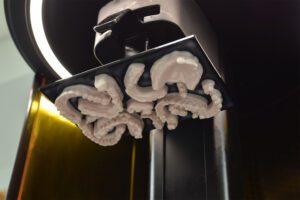
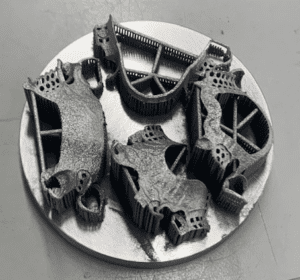